Dorr-Oliver® Flotation Cells
While excellent as an “all around flexible” flotation machine the Dorr-Oliver design is well suited for fine particle recovery with multiple high energy contacts and high bubble surface area flux
Increased Fine Particle Recovery
The Dorr-Oliver Flotation Mechanism is the most energy efficient, technically advanced, forced air flotation machine on the market. It has been specifically designed to maximize fine particle recovery.
The Dorr-Oliver streamlined, high efficiency rotor is a very powerful pump that works together with the stator to generate and define an energy intensive zone in the bottom of the cell. This ensures effective solids suspension and the ability to restart in even the most difficult of applications.
The well defined turbulence zone at the bottom of the cell results in multiple passes of unattached particles through the highest energy dissipation area of the cell where fine particles are driven into contact with the air bubbles.
The stator design, in addition to providing good separation of the zones in the cell also serves to redirect the rotor jet uniformly across the tank to allow the maximum amount of air to be dispersed into the cell without disturbing the surface. Air dispersion capabilities of the Dorr-Oliver cell exceed all competitive forced air designs. Maximizing the air dispersion capability is an important consideration for fine particle recovery. |

|
Improved Froth Handling and High
Concentrate Grade By containing the intense circulation energy at the bottom of the cell the upper zones of the cell remain quiescent to maximize recovery of marginally attached coarse particles and minimize entrainment. The Dorr-Oliver Cell is an exceptional design for cleaner duty.
Dorr-Oliver tank cells are equipped with a uniquely designed high efficiency radial launder system that accelerates the removal of froth as it reaches the surface. Bubble–particle aggregates travel vertically through the froth lattice in essentially plug flow while upgrading. The high efficiency radial launder is shaped to receive the froth uniformly from the cell surface as well as from the typically heavy loaded area near the center of a forced air machine. On passing over the lip the froth is accelerated to the perimeter of the cell. Rarely is launder water a requirement with this unique design. |
 |
-
- Well defined quiescence zone reduces entrainment and gives stable froth
- Concentrate grade is maximized.
- High efficiency radial launder maximizes froth recovery and reduces coarse particle drop back.
- Froth transport is optimized.
SuperCell® Flotation Cells
FLSmidth is pioneering the way for large cell technology with the largest operating cells on the market today. From our first 250m3 cells installed in 2003 to now with up to 350m3 designs and 300m3 cells being installed around the world.
The 350m3 SuperCell™ flotation cell is the largest operating flotation cell in the world with proven performance in hydrodynamics, metallurgy, and mechanical reliability.
FLSmidth has the largest installed based of large cells around the world.
Over 50 of the 300m3 SuperCells have been sold and over 100 of the 250m3 cells have been installed.
The SuperCell Flotation Cells are proven to reduce operating and installation costs as a result of the economies of scale and a reduced foot print with fewer control points. |
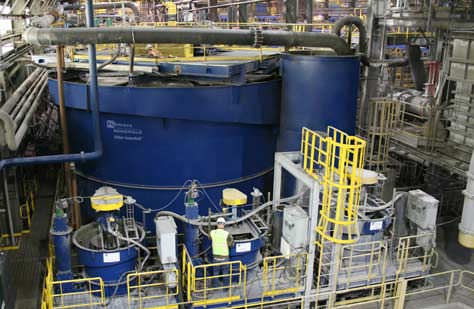 |
Scale up was completed using validated CFD models with comprehensive metallurgical testing at full scale. There is no degradation of metallurgical performance with the SuperCell.
SuperCell benefits include:
-
- Reduced foot print
- Reduced installation cost
- Easier implementation of sophisticated process control
- Equal or better metallurgy
- Proven performance in hydrodynamics, metallurgy, and mechanical reliability
FLSmidth SuperCells use a universal tank that can be fitted with either the Wemco® self aspirated or Dorr-Oliver® forced air designs. This allows SuperCells to be installed as roughers, cleaners and scavengers depending on the requirements of your application.
Taking forced-air flotation to the NEXT STEP
FLSmidth’s nextSTEP™ rotor/stator provides a step change in metallurgical performance and energy efficiency compared to any other forced-air design on the market.
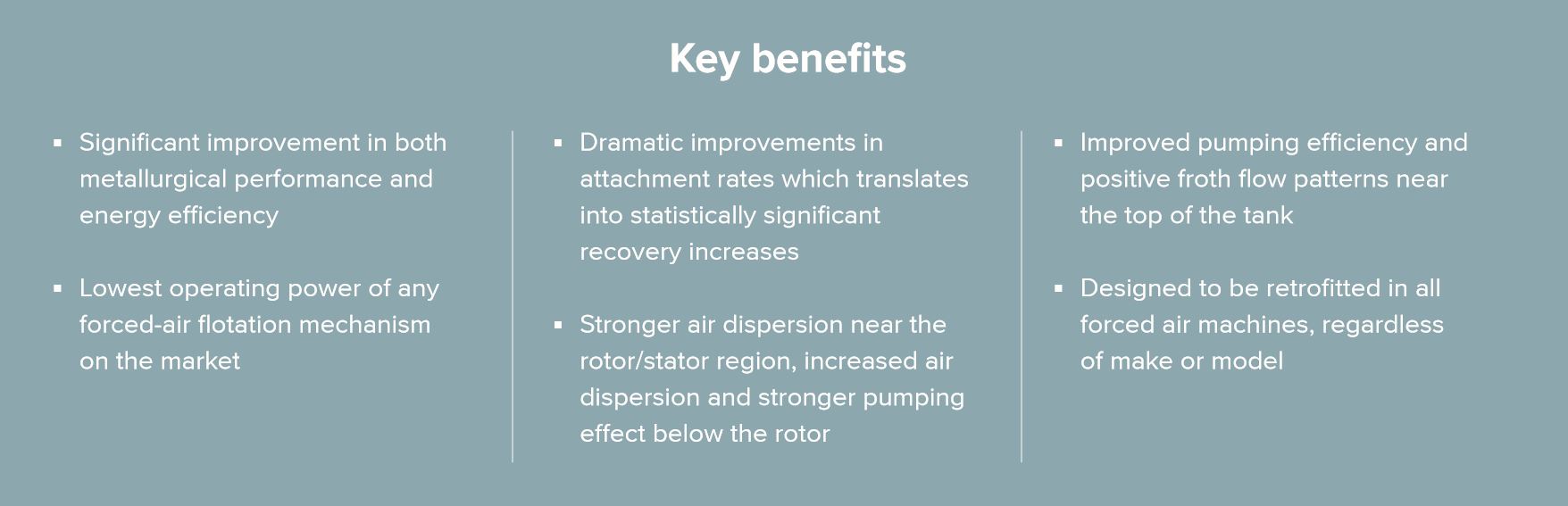
Innovative technology
FLSmidth introduces the patented nextSTEP™ advanced flotation mechanism; the newest design for forced-air flotation technology which reduces operating costs with the lowest power consumption on the market. This new rotor/stator technology is the result of extensive fundamental studies, laboratory test work and full-scale plant testing.
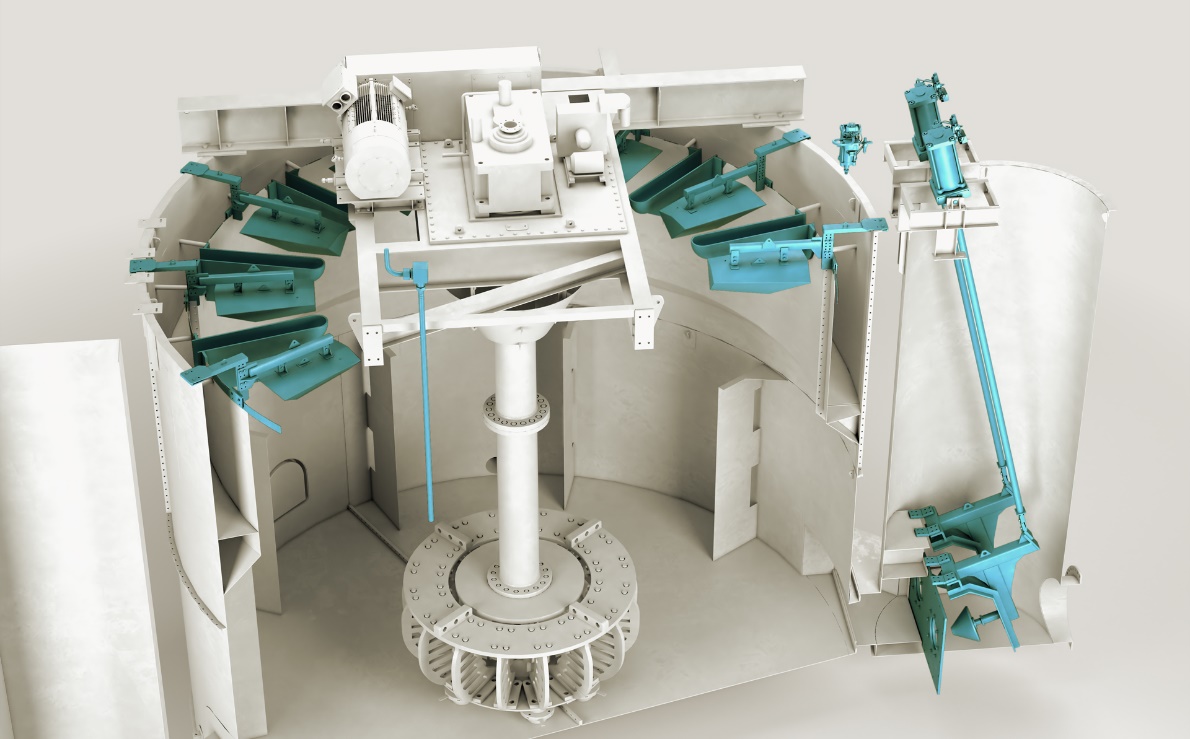
FLSmidth has proven to be the market leader in providing new technology for mineral processing, particularly top-of-the-line flotation equipment. Continuous improvement and development of new products demonstrates FLSmidth’s strong commitment to the minerals market and its customers.
FLSmidth spent four years developing nextSTEP, starting from first principles, using computational fluid dynamic models, and 3D printed prototypes, to optimize the rotor-stator design.
This final technology demonstrates significant improvement in both metallurgical performance and energy efficiency over existing forced-air designs. |
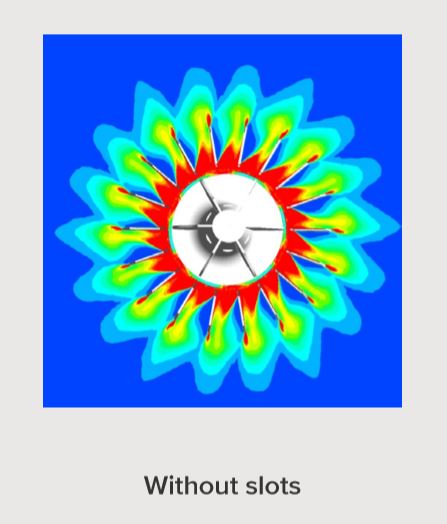 |
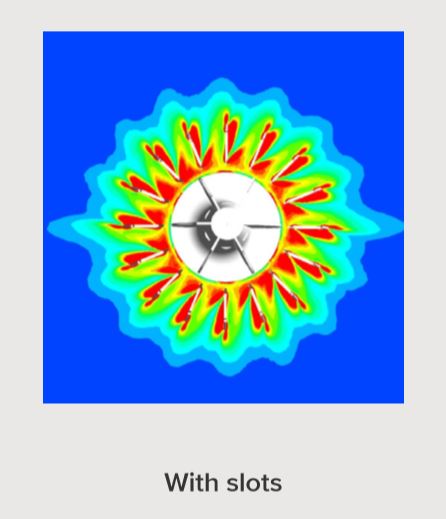 |
CFD Comparison of the turbulence eddy dissipation for stators with and without slots. Slots yield more homogenized turbulence dissipation. |
The exceptional performance of the nextSTEP mechanism comes from the rotor and stator being perfectly matched which delivers the best energy dissipation flow, thus maximizing recovery.
The superior metallurgical performance of the nextSTEP mechanism shows up to a 5% increase in recovery, resulting from dramatic improvements in mineral-bubble attachment rates.
When installed, operators note a 15-40% reduction of power requirements and see better wear distribution for increased rotor/ stator life. These findings have a strong positive impact on total cost of ownership that can benefit both new and existing installations.
Increased flotation
Wide flow jets produced by the nextSTEP rotor and the cross pattern from the patented slotted nextSTEP stator increase the probability of bubble-particle attachment. Adding slots to the stator increases recovery and boosts overall flotation efficiency. One reason for this improvement is the higher homogenized turbulence dissipation energy.
Superior metallurgical performance
In-plant testing of the nextSTEP rotor/ stator combination showed superior metallurgical performance compared to a non-slotted stator design. These results showed dramatic improvement in the attachment rate from the slotted stator design which translates into statistically significant recovery increases.
Improved recovery of coarse particles
When compared to other forced-air flotation designs, the nextSTEP mechanism exhibits stronger air dispersion near the rotor/stator region, higher air hold-up and a stronger pumping effect below the rotor. CFD analysis shows that the nextSTEP mechanism generates a preferred slurry flow and positive froth movement pattern near the top of the tank. This improves froth mobility and recovery of coarse particles over other competitive designs.
Better mixing
Solids suspension tests performed in laboratory, pilot and full-scale conditions exhibited excellent mixing over a wide range of impeller speeds.
Wide flow jets produced by the nextSTEP rotor and the cross pattern from the patented slotted nextSTEP stator increase the chances of flotation |
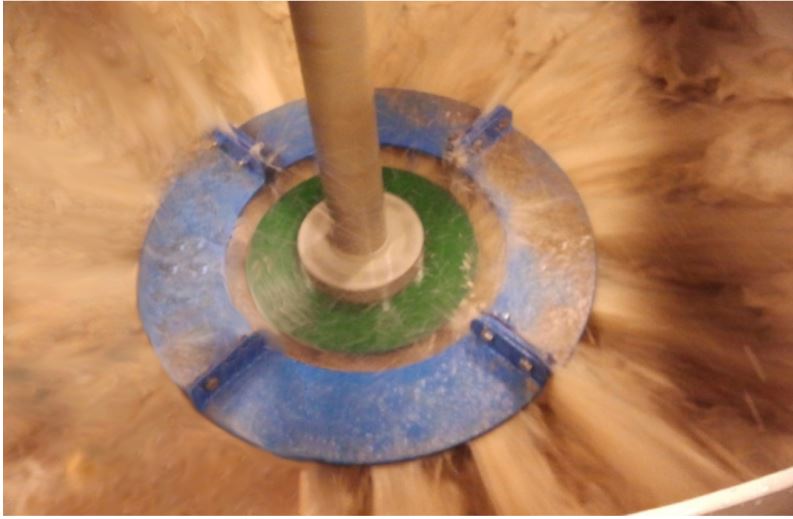 |
Lowest power consumption on the market
The nextSTEP mechanism demonstrates a significant decrease in power consumption in comparison to other flotation technologies and has proven to be the lowest energy flotation mechanism on the market.
The lower energy consumption and the superior metallurgical performance of the nextSTEP mechanism is beneficial for any operation. The nextSTEP mechanism has a strong positive impact on long- term operating costs for greenfield projects. In the case of brownfield projects and existing concentrators, the mechanism is interchangeable with existing FLSmidth forced-air flotation mechanisms and can be retrofitted to all mechanical forced air flotation machines, regardless of make or model. |
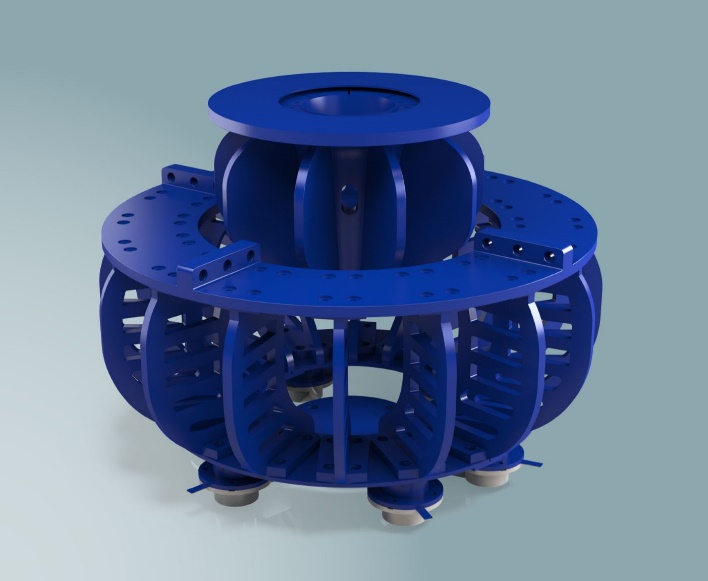 |
Converting to nextSTEP is simple and low risk. The existing mechanism assembly is utilised. Rotor and stator are attached with adaptor flange and baseplate respectively, and drive sheaves replaced to optimise speed. The FLSmidth conversion process is thorough and proven – with a large number of successful retrofits already for flotation cells ranging in size for 1.7m3 to 250m3.
Increased wear life
Several tests performed on the nextSTEP rotor/stator showed a more even wear distribution than other available mechanisms. This increases the life cycle of the mechanism as there are no heavy wear spots during operation. This not only saves money over the life of the rotor/stator, but reduces downtime for repairs or replacements. In addition to even wear patterns, the rotor can be run in a reverse direction to further increase the life cycle of the mechanism. |
 |
The next step in forced-air flotation
FLSmidth is the world’s largest supplier of flotation equipment offering lower energy consumption, improved recovery and increased operational efficiency.
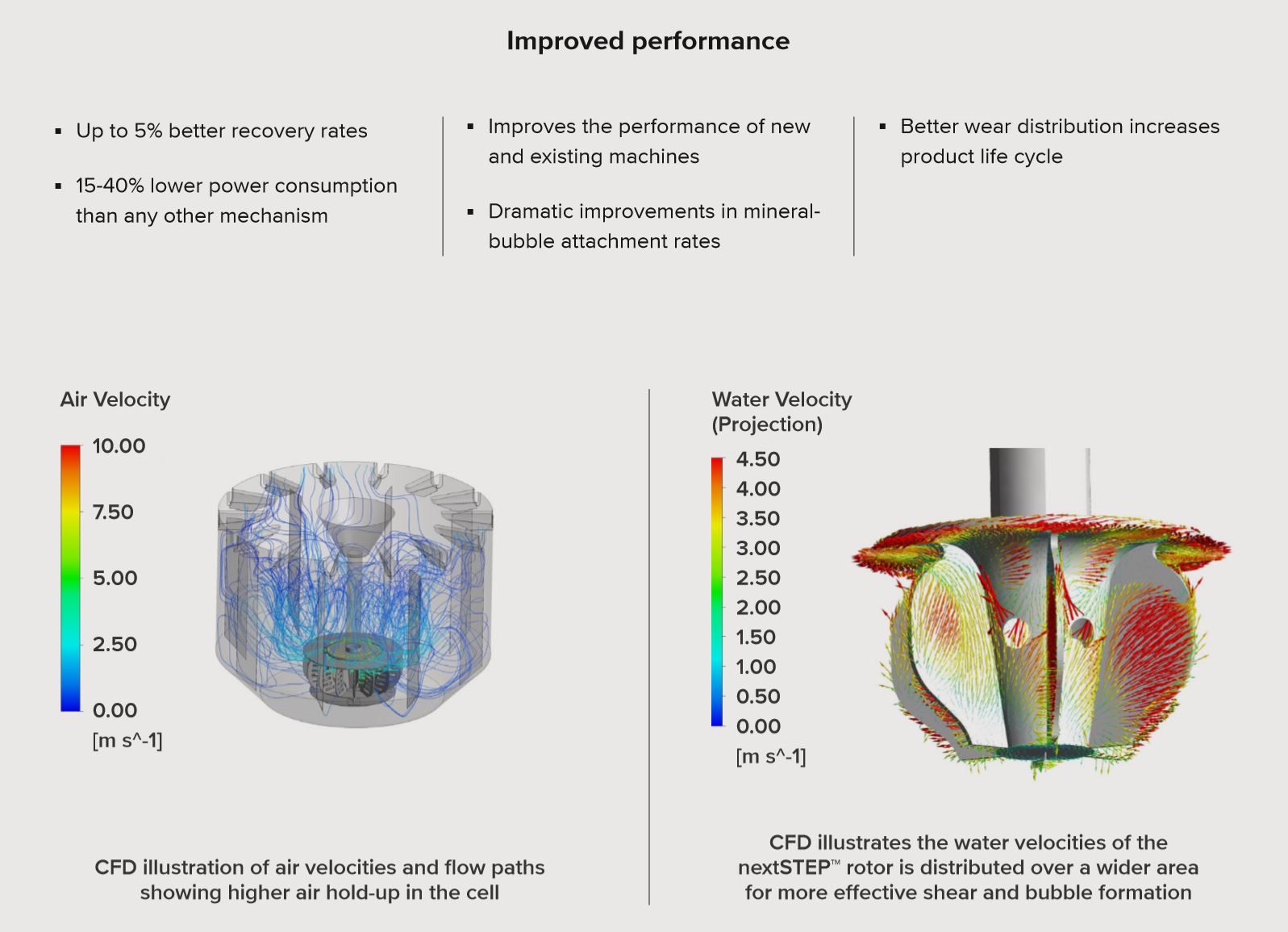
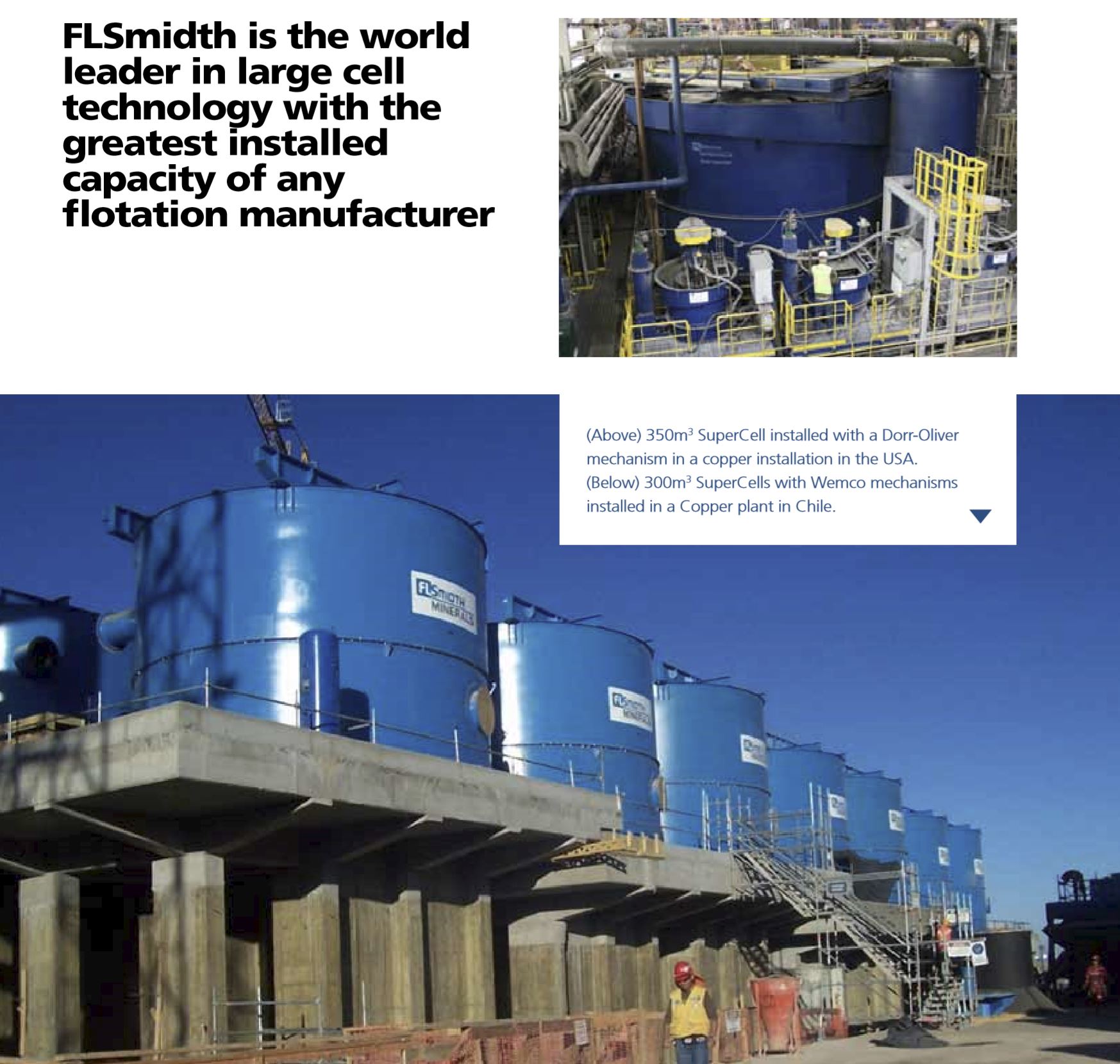
MAJOR FLOTATION APPLICATION
- Minerals industrial: Phophate, Potash, Clays, Coal
- Base Metals: Iron, Copper, Lead, Zinc
- Preciuos Metals: Gold, Platinum and Palladium, Silver, Nickel
- Industrial Processing
- Waste Water Treament
Global Leading Manufactures: |

|